In today's rapidly evolving industrial landscape, Mesta roll grinder modernization has become a pivotal focus for manufacturers seeking to enhance productivity and efficiency. The modernization of Mesta roll grinders not only extends the life of these essential machines but also integrates cutting-edge technologies that improve precision and reduce operational costs. For industries reliant on heavy machinery, staying ahead with modernized equipment is no longer optional—it’s a necessity.
Manufacturers across the globe are increasingly recognizing the importance of upgrading their Mesta roll grinders. These machines, which were once the epitome of engineering excellence, can now be enhanced with state-of-the-art features that cater to the demands of contemporary manufacturing processes. Modernization ensures that these machines remain competitive and relevant in a market characterized by increasing complexity and stringent quality standards.
From improving machine accuracy to reducing downtime and energy consumption, Mesta roll grinder modernization offers a multitude of benefits that directly impact the bottom line. This article delves into the nuances of Mesta roll grinder modernization, exploring its advantages, challenges, and the technologies driving this transformation. Whether you're a seasoned industry professional or simply curious about industrial machinery, this guide will provide valuable insights into the future of roll grinding.
Read also:Back To The Future Repelis A Timeless Adventure Revisited
Understanding Mesta Roll Grinders
History and Evolution of Mesta Roll Grinders
The origins of Mesta roll grinders trace back to the early 20th century when they were first introduced as robust machines designed for heavy-duty grinding applications. Initially, these grinders were primarily used in the steel and mining industries, where their durability and reliability made them indispensable. Over the decades, Mesta roll grinders have undergone several transformations, adapting to the changing needs of industries.
With advancements in metallurgy and manufacturing techniques, Mesta roll grinders have evolved to incorporate more sophisticated components and systems. These enhancements have not only improved the efficiency of the machines but also expanded their applications across various sectors. Understanding the history of Mesta roll grinders provides valuable context for appreciating the significance of their modernization.
Key Components and Features
A Mesta roll grinder is a complex machine composed of several critical components, each playing a vital role in its operation. The primary components include:
- Grinding Wheel: Responsible for the actual grinding process, the grinding wheel is one of the most crucial parts of the machine.
- Spindle Assembly: Ensures precise movement and alignment of the grinding wheel, contributing to the accuracy of the grinding process.
- Workhead: Holds and rotates the workpiece, allowing it to be ground uniformly.
- Hydraulic System: Provides power and control for various machine functions, ensuring smooth and efficient operation.
These components work in tandem to deliver the precision and power required for effective roll grinding. Modernization efforts often focus on upgrading these components with advanced technologies, such as CNC controls and servo drives, to enhance performance.
Benefits of Mesta Roll Grinder Modernization
Improved Precision and Accuracy
One of the most significant advantages of Mesta roll grinder modernization is the improvement in precision and accuracy. By integrating advanced control systems and sensors, modernized grinders can achieve tighter tolerances and better surface finishes. This level of accuracy is crucial for industries that demand high-quality products, such as aerospace and automotive manufacturing.
Increased Productivity
Modernized Mesta roll grinders are equipped with faster processing speeds and enhanced automation capabilities, leading to increased productivity. These machines can handle larger workloads in less time, reducing the overall production cycle and allowing manufacturers to meet higher demand without compromising quality.
Read also:Christopher Hildebrant Cincinnati Profile A Comprehensive Look Into His Life And Achievements
Cost Efficiency
Although the initial investment in modernization can be substantial, the long-term cost savings are significant. Modernized Mesta roll grinders consume less energy, require fewer repairs, and have lower maintenance costs compared to their outdated counterparts. Additionally, the improved efficiency translates into reduced material waste, further contributing to cost savings.
Challenges in Mesta Roll Grinder Modernization
Technical Complexities
Modernizing a Mesta roll grinder involves overcoming several technical challenges. The integration of new technologies with existing systems requires expertise and careful planning to ensure compatibility and functionality. Moreover, the retrofitting process can be intricate, especially when dealing with older machines that may lack the necessary infrastructure for modern components.
Financial Considerations
The cost of modernization can be a significant hurdle for many manufacturers. While the long-term benefits outweigh the initial expenses, the upfront investment can be prohibitive for smaller businesses. It is essential for companies to conduct thorough cost-benefit analyses to determine the feasibility of modernization projects.
Training and Skill Development
With the introduction of advanced technologies, there is a need for operators and maintenance personnel to undergo training to effectively utilize the modernized equipment. This requires additional resources and time, which can impact production schedules and increase operational costs in the short term.
Technologies Driving Mesta Roll Grinder Modernization
CNC Controls and Automation
Computer Numerical Control (CNC) systems are at the forefront of Mesta roll grinder modernization. These systems enable precise control over the grinding process, allowing for complex operations to be performed with minimal human intervention. Automation not only enhances accuracy but also improves consistency and repeatability, ensuring uniform quality across all products.
Servo Drives and Motors
Servo drives and motors are integral to the modernization of Mesta roll grinders. They provide superior speed and torque control, enabling the machines to operate more efficiently and with greater precision. The use of servo technology reduces energy consumption and wear on machine components, extending the lifespan of the grinder.
Data Analytics and IoT Integration
The integration of data analytics and Internet of Things (IoT) technologies allows for real-time monitoring and analysis of machine performance. This enables predictive maintenance, reducing unexpected downtime and optimizing machine usage. By leveraging data insights, manufacturers can make informed decisions to enhance productivity and efficiency.
Case Studies: Successful Mesta Roll Grinder Modernization
Company A: Enhancing Steel Production
Company A, a leading steel manufacturer, successfully modernized its fleet of Mesta roll grinders, resulting in a 25% increase in productivity. By implementing CNC controls and servo drives, the company achieved higher precision and reduced energy consumption by 15%. The modernization project not only improved operational efficiency but also enhanced product quality, leading to increased customer satisfaction.
Company B: Reducing Downtime in Mining Operations
Company B, a mining equipment manufacturer, faced frequent downtime due to the aging infrastructure of its Mesta roll grinders. Through modernization, the company incorporated IoT sensors and predictive analytics, reducing unplanned downtime by 30%. This improvement allowed the company to meet production targets more consistently and improve its overall profitability.
Best Practices for Mesta Roll Grinder Modernization
Conducting a Feasibility Study
Before embarking on a modernization project, it is crucial to conduct a feasibility study to assess the potential benefits and challenges. This study should include a detailed analysis of the current machine condition, production requirements, and budget constraints. By understanding these factors, manufacturers can make informed decisions about the scope and scale of the modernization project.
Partnering with Experienced Suppliers
Collaborating with experienced suppliers and integrators can significantly enhance the success of a Mesta roll grinder modernization project. These partners bring valuable expertise and resources to the table, ensuring that the modernization process is executed efficiently and effectively. They can also provide ongoing support and maintenance services to maximize the lifespan of the upgraded equipment.
Investing in Operator Training
Training operators and maintenance personnel is a critical component of successful modernization. By investing in comprehensive training programs, manufacturers can ensure that their workforce is equipped with the necessary skills to operate and maintain the modernized equipment. This not only improves machine utilization but also enhances overall productivity.
Future Trends in Mesta Roll Grinder Modernization
Artificial Intelligence and Machine Learning
The future of Mesta roll grinder modernization lies in the integration of artificial intelligence (AI) and machine learning (ML) technologies. These technologies have the potential to revolutionize the grinding process by enabling autonomous decision-making and continuous improvement. AI-driven systems can optimize machine settings in real-time, ensuring optimal performance and reducing the need for manual adjustments.
Sustainable Manufacturing Practices
As environmental concerns continue to grow, manufacturers are increasingly focusing on sustainable manufacturing practices. Modernized Mesta roll grinders can contribute to this effort by reducing energy consumption and minimizing waste. The adoption of eco-friendly technologies and materials will play a vital role in shaping the future of roll grinding.
Conclusion
Mesta roll grinder modernization is a transformative process that offers numerous benefits for manufacturers seeking to enhance productivity and efficiency. By upgrading their machines with advanced technologies, companies can achieve higher precision, increased productivity, and cost savings. While challenges such as technical complexities and financial considerations exist, the long-term advantages of modernization far outweigh the initial investments.
We encourage readers to explore the possibilities of Mesta roll grinder modernization and consider implementing these technologies in their operations. For more insights into industrial machinery and modernization, please feel free to leave a comment or share this article with your network. Together, we can drive the future of manufacturing forward.
Table of Contents
- Understanding Mesta Roll Grinders
- Benefits of Mesta Roll Grinder Modernization
- Challenges in Mesta Roll Grinder Modernization
- Technologies Driving Mesta Roll Grinder Modernization
- Case Studies: Successful Mesta Roll Grinder Modernization
- Best Practices for Mesta Roll Grinder Modernization
- Future Trends in Mesta Roll Grinder Modernization
- Conclusion
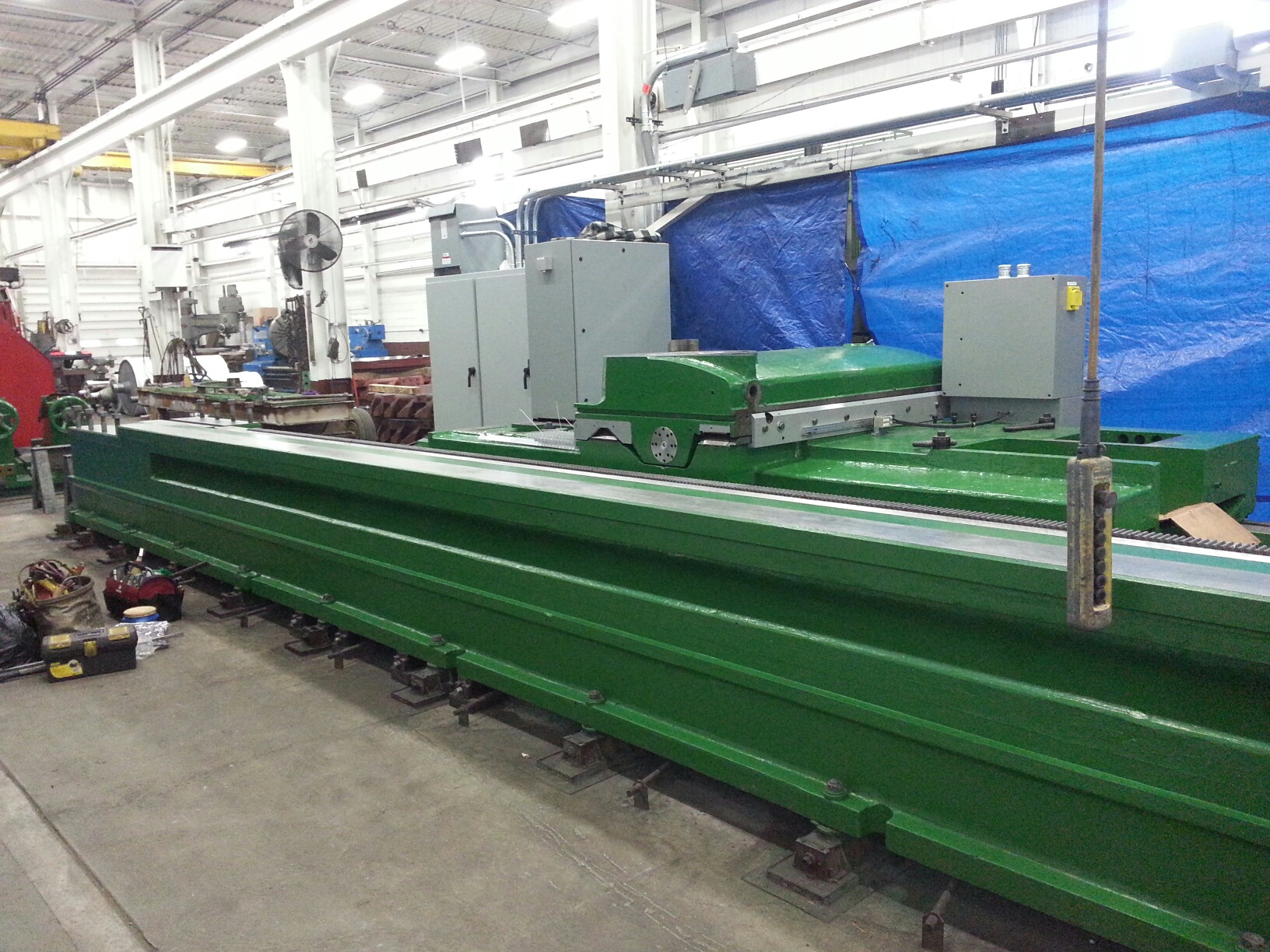
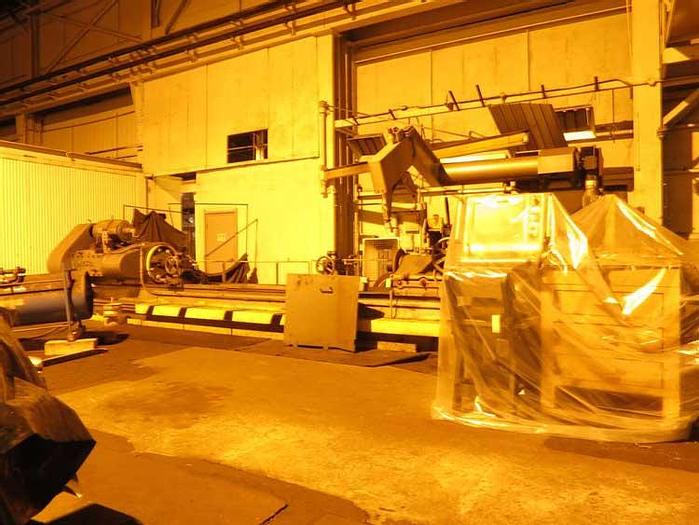