Roll grinding is a critical manufacturing process that enhances the surface finish and dimensional accuracy of cylindrical components. This technique plays a vital role in industries such as automotive, aerospace, and metalworking, ensuring components meet stringent quality standards. As technology evolves, the importance of mastering roll grinding techniques has never been more significant.
In today's competitive industrial landscape, precision engineering is the backbone of successful manufacturing operations. Roll grinding, in particular, is a highly specialized process that demands expertise, advanced machinery, and meticulous attention to detail. This article delves into the intricacies of roll grinding, offering insights into its applications, benefits, and best practices.
Whether you're a manufacturing professional, an engineer, or a student exploring the world of precision machining, this guide will provide you with the knowledge and tools necessary to excel in roll grinding. By understanding the principles behind this process, you'll be better equipped to optimize your operations and achieve superior results.
Read also:Does Kensley Pope Have 3 Boobs Separating Fact From Fiction
Understanding Roll Grinding: An Overview
Roll grinding is a machining process that involves the use of abrasive wheels to shape and refine cylindrical components. The primary objective of this technique is to achieve precise dimensions, smooth surfaces, and enhanced durability. This section explores the fundamental aspects of roll grinding, including its definition, purpose, and significance in modern manufacturing.
One of the key advantages of roll grinding is its ability to remove minimal material while achieving remarkable precision. This makes it an ideal solution for applications where maintaining tight tolerances is essential. Additionally, the process enhances the fatigue resistance and load-bearing capabilities of components, making it indispensable in industries that demand high-performance parts.
Applications of Roll Grinding
Roll grinding finds extensive use across various sectors, including:
- Automotive manufacturing
- Aerospace engineering
- Metalworking industries
- Tool and die production
Each of these industries relies on roll grinding to produce components that meet exacting specifications, ensuring safety, reliability, and longevity.
Key Components of Roll Grinding Machines
A roll grinding machine consists of several critical components that work in harmony to achieve optimal results. Understanding these components is essential for anyone seeking to master the art of roll grinding. Below is a detailed breakdown of the primary elements involved in the process:
Grinding Wheels
Grinding wheels are the heart of any roll grinding operation. These wheels are composed of abrasive particles bonded together with a matrix material. The choice of abrasive material depends on the material being ground and the desired finish. Common abrasive materials include:
Read also:Contact Tatasecorg A Comprehensive Guide To Reaching Out
- Aluminum oxide
- Silicon carbide
- Diamond
- Cubic boron nitride (CBN)
Each abrasive type offers unique properties, such as hardness, heat resistance, and cutting efficiency, making it suitable for specific applications.
Workhead and Tailstock
The workhead and tailstock are crucial components that secure and rotate the workpiece during the grinding process. These parts ensure the workpiece remains stable and aligned, facilitating accurate grinding operations. Advanced roll grinding machines often incorporate CNC technology to enhance precision and automation.
Advantages of Roll Grinding
Roll grinding offers numerous benefits that make it a preferred choice for precision machining. Some of the key advantages include:
- Superior surface finish
- Improved dimensional accuracy
- Enhanced fatigue resistance
- Increased load-bearing capacity
- Reduced material removal
By leveraging these benefits, manufacturers can produce high-quality components that meet or exceed industry standards, ultimately driving operational efficiency and customer satisfaction.
Common Challenges in Roll Grinding
Despite its numerous advantages, roll grinding is not without its challenges. Common issues that operators may encounter include:
- Wheel wear and dressing
- Thermal damage to the workpiece
- Vibration and chatter
- Surface defects
Addressing these challenges requires a combination of proper machine maintenance, operator training, and the use of advanced technologies. Regular wheel dressing, for example, ensures consistent performance and minimizes wear, while vibration-dampening systems help maintain stability during operations.
Best Practices for Roll Grinding
Implementing best practices is essential for achieving optimal results in roll grinding. Below are some key recommendations:
Machine Calibration and Maintenance
Regular calibration and maintenance of roll grinding machines are critical for ensuring consistent performance. Operators should adhere to the manufacturer's guidelines for servicing and inspecting machines, paying particular attention to components such as grinding wheels, bearings, and spindle systems.
Operator Training and Skill Development
Skilled operators play a pivotal role in the success of any roll grinding operation. Providing comprehensive training programs that cover machine operation, troubleshooting, and safety protocols is essential for maximizing productivity and minimizing errors.
Roll Grinding Techniques and Innovations
Advancements in technology have led to the development of innovative roll grinding techniques that enhance efficiency and precision. Some of the latest innovations include:
CNC-Controlled Roll Grinding
CNC (Computer Numerical Control) technology has revolutionized the roll grinding process by enabling automated operations with unparalleled accuracy. CNC machines can execute complex grinding patterns and adjustments with minimal human intervention, significantly reducing cycle times and improving part quality.
Grinding Wheel Advancements
Recent developments in grinding wheel technology have introduced new materials and coatings that enhance performance and durability. For example, superabrasive wheels made from diamond and CBN offer superior cutting efficiency and longer service life, making them ideal for challenging applications.
Applications of Roll Grinding in Various Industries
The versatility of roll grinding makes it applicable across a wide range of industries. Below are some examples of how this process is utilized in different sectors:
Automotive Industry
In the automotive sector, roll grinding is employed to produce components such as crankshafts, camshafts, and bearing journals. The process ensures these parts meet stringent quality standards, contributing to the overall performance and reliability of vehicles.
Aerospace Engineering
Aerospace applications demand components with exceptional precision and durability. Roll grinding is used to manufacture turbine blades, shafts, and other critical parts, ensuring they can withstand extreme operating conditions.
Data and Statistics Supporting Roll Grinding
According to industry reports, the global market for roll grinding equipment is projected to grow at a compound annual growth rate (CAGR) of 5.2% over the next decade. This growth is driven by increasing demand for precision machining in various industries, coupled with advancements in grinding technology.
Furthermore, studies indicate that roll grinding can improve surface finish by up to 80% compared to traditional machining methods, while reducing material removal by 30%. These statistics highlight the significant benefits of adopting roll grinding techniques in manufacturing operations.
Future Trends in Roll Grinding
As technology continues to evolve, several trends are expected to shape the future of roll grinding:
- Increased adoption of Industry 4.0 technologies, such as IoT and AI
- Development of eco-friendly grinding materials and processes
- Integration of predictive maintenance systems
- Enhanced focus on energy efficiency
By embracing these trends, manufacturers can stay ahead of the competition and meet the growing demands of the global market.
Conclusion: Elevate Your Roll Grinding Operations
In conclusion, roll grinding is a vital process that plays a crucial role in modern manufacturing. By understanding its principles, applications, and best practices, you can optimize your operations and achieve superior results. The advancements in technology and growing demand for precision machining make roll grinding an indispensable tool for industries worldwide.
We invite you to share your thoughts and experiences with roll grinding in the comments section below. Additionally, feel free to explore our other articles for more insights into precision engineering and manufacturing. Together, let's continue to push the boundaries of what's possible in the world of machining!
Table of Contents
- Understanding Roll Grinding: An Overview
- Key Components of Roll Grinding Machines
- Advantages of Roll Grinding
- Common Challenges in Roll Grinding
- Best Practices for Roll Grinding
- Roll Grinding Techniques and Innovations
- Applications of Roll Grinding in Various Industries
- Data and Statistics Supporting Roll Grinding
- Future Trends in Roll Grinding
- Conclusion: Elevate Your Roll Grinding Operations
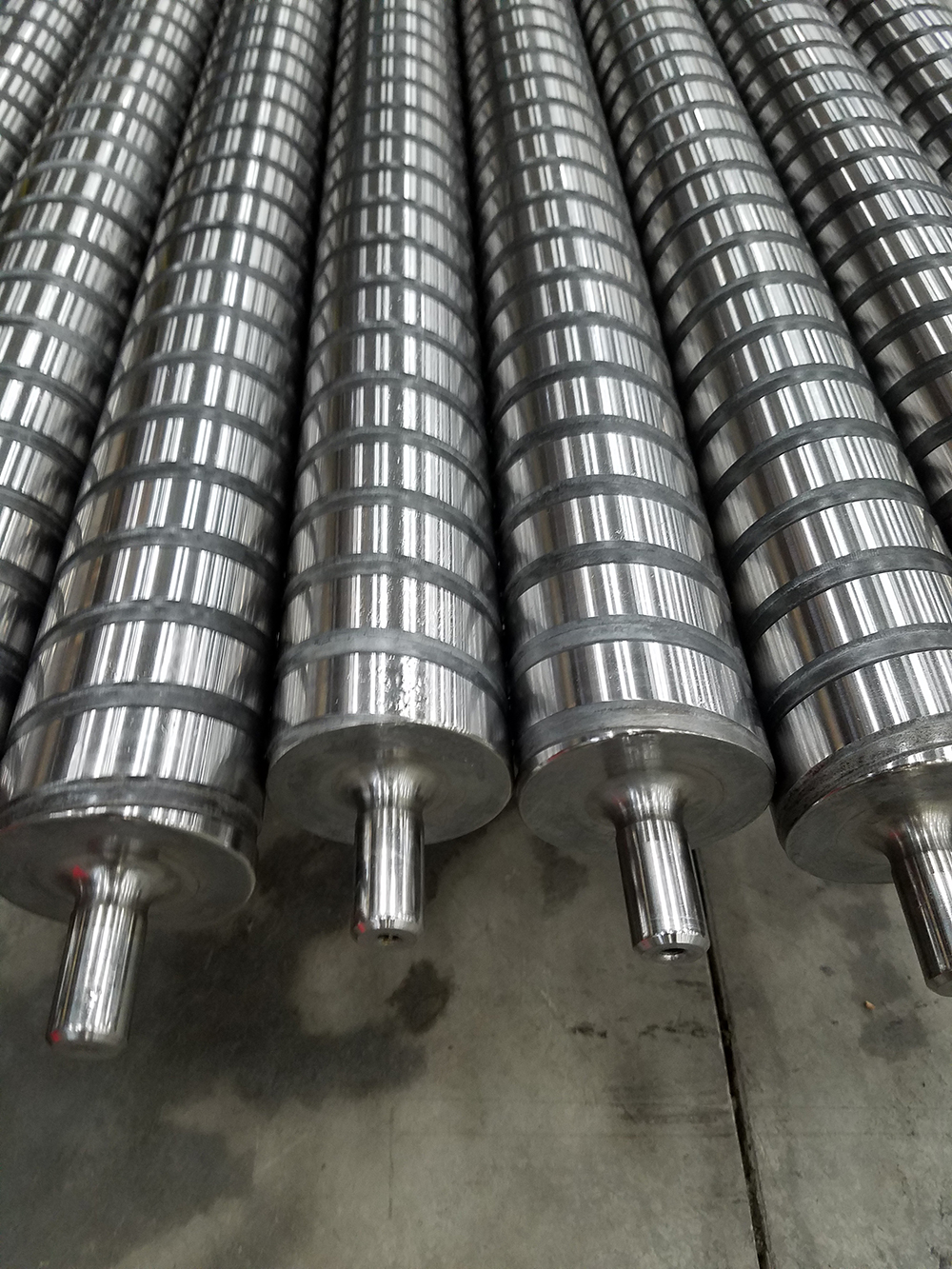

